?stenitik paslanmaz ?elik, yüksek krom i?eri?i ve yo?un oksit filmi nedeniyle iyi bir korozyon direncine sahiptir. Cr18% ve Ni8% i?erildi?inde tek bir ?stenit yap?s? elde edilebilir. Bu nedenle ?stenitik paslanmaz ?elik, iyi korozyon direncine, plastisiteye, yüksek s?cakl?k performans?na ve kaynak performans?na sahiptir. Bununla birlikte, farkl? ?al??ma ko?ullar? alt?nda, ?stenitik paslanmaz ?elik kaynak ba?lant?lar? genellikle, taneler aras? korozyon, stres korozyonu, b??ak korozyonu, kaynak s?cak ?atlaklar?, α faz? gevrekli?i ve benzeri gibi yap? kusurlar?na neden olmas? kolay olan baz? ?zel problemlerle kar?? kar??yad?r.
Kaynakl? ba?lant?lar?n korozyon analizi
Kaynakl? ba?lant?lar?n taneler aras? korozyonu
Taneler aras? korozyon, ?stenitik paslanmaz ?eli?in en ?nemli korozyon problemlerinden biridir. Taneler aras? korozyon meydana geldi?inde, ciddi oldu?unda gücü neredeyse kaybedecek ve belirli bir stres uyguland???nda taneler aras? k?r?lma meydana gelecektir. ?stenitik paslanmaz ?elik kaynak ba?lant?s?n?n taneler aras? korozyonuna esas olarak krom karbür ??keltmesi neden olur. ?stenitik paslanmaz ?elik, 500 ~ 800 ℃ s?cakl?k aral???nda duyarl? hale getirildi?inde, a??r? doymu? kat? ??zelti karbonunun taneler aras? s?n?ra difüzyon h?z?, kromunkinden daha h?zl?d?r ve a??r? doymu? kat? ??zeltideki karbon, tane yak?n?nda krom ile birle?tirilir. B?lgedeki krom i?eri?i pasivasyon i?in gerekli olan limit i?eri?in (w (CR) 12.5%) alt?na dü?tü?ünde b?lgenin korozyonu h?zlanacak ve taneler aras? korozyon olu?acakt?r. Sonu?lar, HAZ'?n hassasla?t?r?lm?? s?cakl?k b?lgesindeki taneler aras? korozyonun, tepe ?s?tma s?cakl???n?n 600 ℃ ile 1000 ℃ aras?nda oldu?u b?lgede meydana geldi?ini g?stermektedir. Taneler aras? korozyonun nedeni, hala ?stenit tane s?n?r?nda krom karbürün ??kelmesidir. Taneler aras? korozyonu azaltmak ve ?nlemek i?in ana ?nleyici tedbirler ?unlar? i?erir:
① Kü?ük ?zellikler (kü?ük ak?m, yüksek kaynak h?z?) ve ?ok pasolu kaynak benimsenmi?tir;
② Ana metal ve kaynak malzemesindeki karbon i?eri?i mümkün oldu?unca azalt?lmal? ve C i?eri?i 0.03%'den az olan kaynak malzemesi kullan?lmal?d?r;
③ Sonu? olarak, Cr, ostenit tane s?n?r?ndaki zay?f krom olgusunu azaltan, ferritte ostenite g?re daha h?zl? tane s?n?r?na yay?l?r;
④ ?elik ve kaynak malzemelerinde karbona kromdan daha gü?lü afiniteye sahip Ti, Nb ve di?er elementlerin eklenmesi, karbon ba?? ile kararl? bile?ikler olu?turabilir, b?ylece ?stenit tane s?n?rlar?nda krom tükenmesini ?nleyebilir.
Kaynakl? ba?lant?lar?n gerilim korozyonu
Paslanmaz ?eli?in gerilmeli korozyon ?atlamas? en zararl? korozyon davran???d?r. ?atlama s?ras?nda deformasyon olmaz. Kaza genellikle ani olur ve sonu?lar? ciddidir. ?eli?in bile?imi, yap?s? ve durumu, ortam?n türü, s?cakl?k, konsantrasyon, stres ?zellikleri, boyut ve yap?sal ?zellikler dahil olmak üzere hizmet ko?ullar? alt?nda paslanmaz ?eli?in gerilme korozyon ?atlamas?n? etkileyen bir?ok fakt?r vard?r.
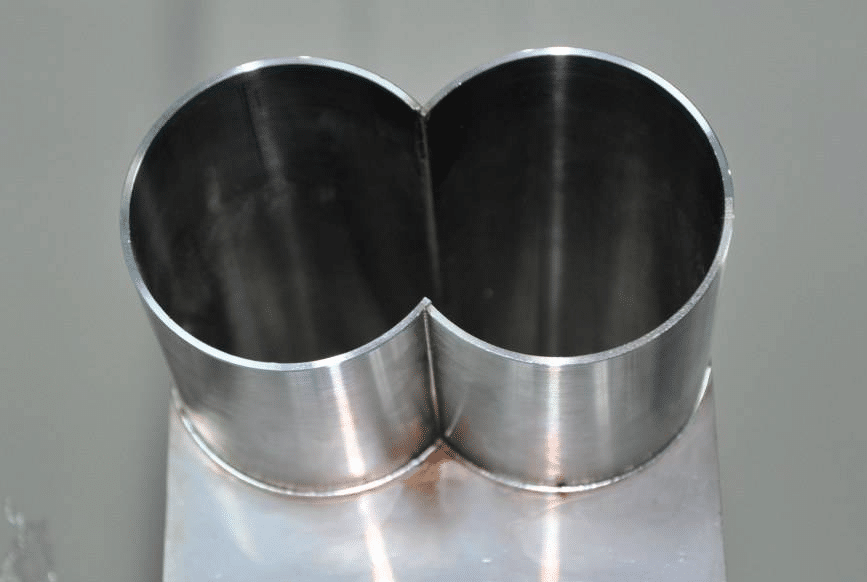
Gerilme korozyonunu azaltmak ve ?nlemek i?in ba?l?ca ?nlemler ?unlard?r:
① Gü?lü montaj, mekanik darbe ve ark yanmas?ndan ka??n?n, so?uk i? deformasyonunu ve stresi azalt?n;
② Ortamdaki ve ortamdaki safs?zl?klar? (?zellikle klorür, florür vb.) s?k? bir ?ekilde kontrol edin;
③ Makul malzeme se?imi (ana metal, kaynak malzemesi): tane irile?mesini ve martensit yap?s?n? sertle?tirmeyi ?nleyin;
④ Kaynak, herhangi bir gerilim konsantrasyonu (alttan kesme gibi) olmadan iyi ?ekillendirilmi?tir;
⑤ Stresi azaltmak i?in kaynak s?ras?n? makul bir ?ekilde düzenleyin;
⑥ Korozyon ?nleyici i?lem: kaplama, astar veya katodik korumaya korozyon ?nleyici ekleyin.
Kaynakl? ba?lant?lar?n s?cak ?atlak hassasiyet analizi
?stenitik paslanmaz ?eli?in s?cak ?atlaklar?, esas olarak, kaynak metalinin s?v? metalinin kat?la?ma i?lemi s?ras?nda üretilen kristal ?atlaklard?r. Bu zamanda, birincil kristaller ?tektik erime noktas?nda, esas olarak dendritler aras?nda bulunur. Ana nedenler a?a??daki gibidir:
① S, P, C ve benzeri, Ni ile dü?ük erime noktal? ?tektik olu?turur (?rne?in, NIS + Ni'nin erime noktas? 644 ℃'dir), bu da tane s?n?r? kuvvetini zay?flat?r;
② ?stenitik paslanmaz ?elik, likidus ve solidus aras?nda büyük mesafe, uzun kristalle?me süresi, gü?lü dendrit oryantasyonu ve safs?zl?k elementlerinin ayr?lmas?n?n kolay üretilmesi gibi avantajlara sahiptir;
③ ?eli?in ?s?l iletkenli?i kü?üktür ve do?rusal genle?me katsay?s? büyüktür, bu nedenle stres üretmek kolayd?r.
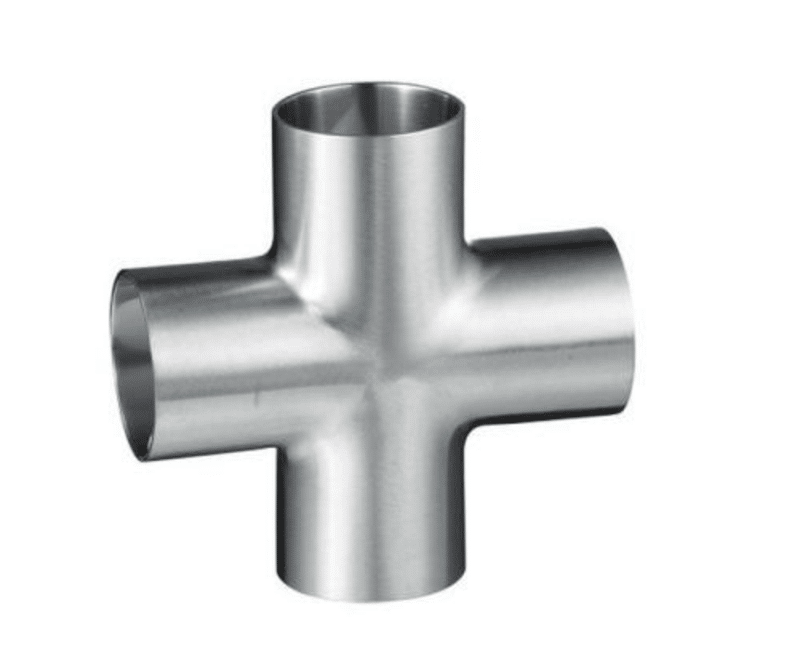
S?cak ?atlaklar?n kaynaklanmas?n? ?nlemek i?in ana ?nlemler ?unlar? i?erir:
① Adi metal ve kaynak malzemesindeki zararl? kükürt ve fosfor safs?zl?klar?n?n i?eri?i s?k? bir ?ekilde kontrol edilecektir;
② Kaynakta, ?stenit sütunlu kristalin y?nünü bozan yakla??k 5% ferrit üretilir;
③ Kü?ük ak?m ve h?zl? kaynak i?lemi benimsenmi?tir.
Kaynakl? ba?lant?larda ferrit i?eri?inin kontrolü
?stenitik ?eli?in kaynak metalindeki ferrit i?eri?i, sadece α (σ) faz gevrekli?inin olu?umu ve termal mukavemeti ile ilgili de?ildir, ayn? zamanda eklemin s?cak ?atlama direncini de do?rudan etkiler. Is?tma süresi ne kadar uzun olursa, yüksek s?cakl?kta kalma süresi o kadar uzun olur, daha fazla ya???, eklemin mekanik ?zelliklerini ciddi ?ekilde etkiler. S?cak ?atlama direnci a??s?ndan, kaynak metalinde belirli bir miktar ferrit gereklidir. Ancak, α faz? gevrekli?i ve termal dayan?m g?z ?nüne al?nd???nda, ferrit i?eri?i ne kadar dü?ükse o kadar iyidir. Bu nedenle, yüksek s?cakl?k dayan?ml? kaynakl? ba?lant?lar i?in ferrit i?eri?i s?k? bir ?ekilde kontrol edilmelidir. Baz? durumlarda ?stenitik kaynak metali kullan?lmal?d?r.
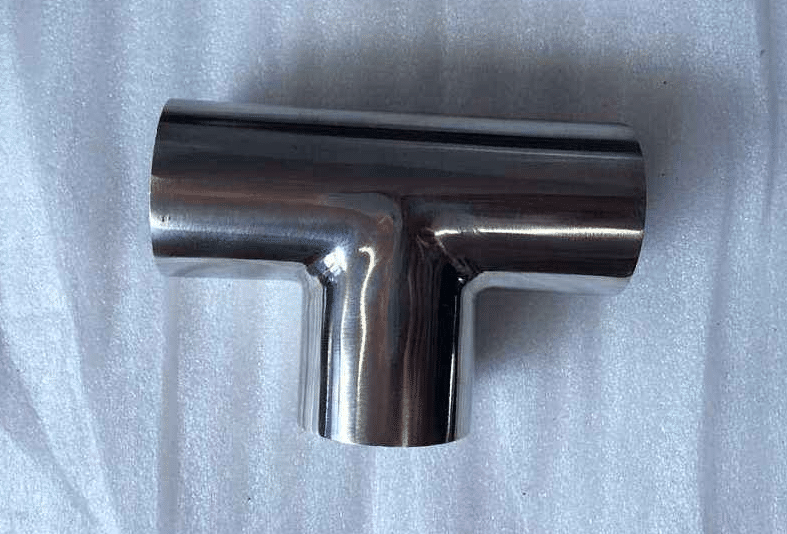