1.極低溫処理プロセスの開発
極低溫処理は通常、液體窒素冷卻を採用しており、ワークピースを-190℃以下に冷卻できます。処理された材料の微細構(gòu)造は低溫で変化し、いくつかの特性が改善されます。極低溫処理は、1939 年に舊ソ連によって最初に提案されました。米國が極低溫処理技術(shù)を産業(yè)に適用し、主に航空分野で使用し始めたのは 1960 年代になってからです。 1970年代には機械製造分野に進出。
冷卻方式の違いにより、液體方式と気體方式に分けられます。液體法とは、材料またはワークを液體窒素に直接浸してワークを液體窒素溫度まで冷卻し、ワークをこの溫度に一定時間保持した後、ワークを取り出して特定の溫度まで加熱することを意味します.このように昇溫?降溫速度を制御することは難しく、ワークへの熱影響が大きく、一般的にワークへのダメージが発生しやすいとされています。極低溫設(shè)備は液體窒素タンクなど比較的シンプルです。
2.極低溫処理のガス法
ガス原理は、液體窒素のガス化潛熱(約199.54kJ/kg)と低溫窒素の吸熱により冷卻するものです。ガス法は、極低溫窒素が材料に接觸できるように、極低溫を-190℃に到達させることができます。対流熱交換により、窒素はノズルから放出された後、極低溫ボックス內(nèi)で気化することができます。ガス化潛熱と極低溫窒素の吸熱により、ワークを冷卻することができます。液體窒素の投入量を制御して冷卻速度を制御することにより、極低溫処理溫度を自動調(diào)整し、正確に制御することができ、熱衝撃の影響が小さく、ひび割れの可能性も低くなります。
現(xiàn)在、ガス法はその応用において研究者によって広く認識されており、その冷卻裝置は主に制御可能な溫度を備えたプログラム可能な極低溫ボックスです。極低溫処理は、鉄金屬、非鉄金屬、金屬合金、およびその他の材料の耐用年數(shù)、耐摩耗性、および寸法安定性を大幅に改善し、かなりの経済的利益と市場の見通しをもたらします。
超硬合金の極低溫技術(shù)は、1980 年代と 1990 年代に初めて報告されました。 機械技術(shù) 1981 年に日本の 現(xiàn)代の機械工場 1992 年に米國の は、極低溫処理後に超硬合金の性能が大幅に向上したことを報告しました。 1970 年代以降、海外での極低溫治療に関する研究は実り多いものでした。舊ソ連、米國、日本、その他の國では、極低溫処理を使用して工具や金型の耐用年數(shù)、ワークピースの耐摩耗性、寸法安定性を向上させることに成功しています。
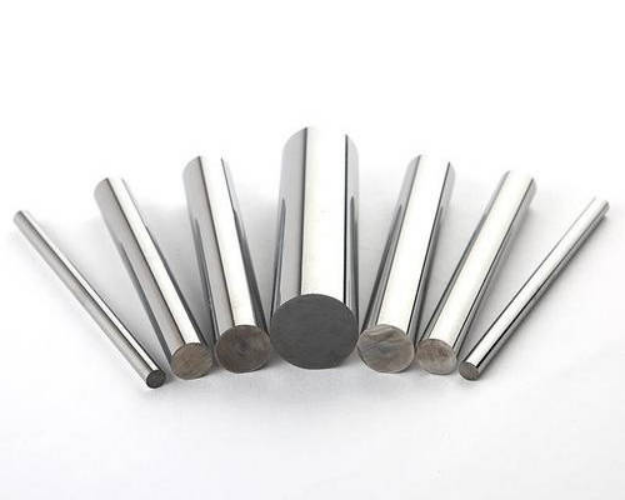
3.極低溫処理のメカニズム強化
金屬相強化。
超硬合金中の Co は、fcc 結(jié)晶構(gòu)造 α 相 (fcc) と最密六方晶構(gòu)造 ε 相 (hcp) を持っています。 ε-Co比率 α-Coは摩擦係數(shù)が小さく、耐摩耗性に優(yōu)れています。 417 ℃以上 α 相の自由エネルギーが低いため、Co α 相の形態(tài)が存在する。 417℃以下 ε相の低自由エネルギー、高溫で安定相 α相から低自由エネルギーε相へ相転移。しかし、WC粒子とαにより、相中に固溶ヘテロ原子が存在するため、相転移に対する制約が大きくなり、α→εとなり、相変化抵抗が増加し、溫度が417℃を下回ると、α 相が完全に変換できなくなります。 εフェーズに。極低溫処理は大幅に増加させることができます α と ε 二相の自由エネルギー差、したがって、相変化の駆動力 ε 相変化変數(shù)を増加させます。極低溫処理後の超硬合金では、溶解度の低下により Co に溶解していた一部の原子が化合物の形で析出し、Co マトリックスの硬質(zhì)相を増加させ、転位の移動を妨げ、第 2 相を強化する役割を果たします。粒子。
表面殘留応力の強化。
極低溫処理後の研究は、表面の殘留圧縮応力が増加することを示しています。多くの研究者は、表面層に一定の値の殘留圧縮応力があれば、その耐用年數(shù)を大幅に改善できると考えています。焼結(jié)後の超硬合金の冷卻過程で、結(jié)合相のCoは引張応力を受け、WC粒子は圧縮応力を受けます。引張応力はCoに大きなダメージを與えます。したがって、一部の研究者は、深い冷卻によって引き起こされる表面圧縮応力の増加が、焼結(jié)後の冷卻プロセス中に結(jié)合相によって生成される引張応力を遅くするか、部分的に相殺するか、またはそれを調(diào)整することさえあると信じています。圧縮応力、マイクロクラックの発生を減らします。
その他の強化メカニズム
η 相粒子は WC 粒子とともにマトリックスをよりコンパクトで強固にし、η により、相の形成はマトリックス中の Co を消費すると考えられています。結(jié)合相のCo含有量が減少すると、材料の全體的な熱伝導(dǎo)率が増加し、炭化物の粒子サイズと隣接度が増加すると、マトリックスの熱伝導(dǎo)率も増加します。熱伝導(dǎo)率の増加により、ツールとダイの先端の熱放散が速くなります。工具や金型の耐摩耗性と高溫硬度が向上します。極低溫処理後、Co の収縮と緻密化により、WC 粒子を保持する Co の確固たる役割が強化されると考える人もいます。物理學(xué)者は、深い冷卻が金屬の原子と分子の構(gòu)造を変えたと信じています。
4.極低溫処理を施したYG20冷間圧造型の事例
YG20 コールド ピア型枠極低溫処理の操作手順:
(1) 焼結(jié)冷間圧造用金型を極低溫処理爐に入れる。
(2) 低溫?zé)啈芬惑w型爐を始動し、液體窒素を開放し、一定の速度で-60 ℃まで下げ、その溫度を 1 時間維持します。
(3) 一定の速度で-120 ℃まで下げ、その溫度を 2 時間保持します。
(4) 一定の冷卻速度で溫度を – 190 ℃ まで下げ、その溫度を 4 ~ 8 時間維持します。
(5) 保溫後、0.5℃/minで180℃まで4時間昇溫する。
(6) プログラム裝置が完成すると、自動的に電源が切れ、室溫まで自然冷卻されます。
結(jié)論: 極低溫処理なしの YG20 冷間圧造ダイスと極低溫処理後の冷間圧造 Φ 3.8 炭素鋼スクリュー ロッドは、極低溫処理後の金型の耐用年數(shù)が、極低溫処理なしの金型よりも 15% 以上長いことを示しています。 .
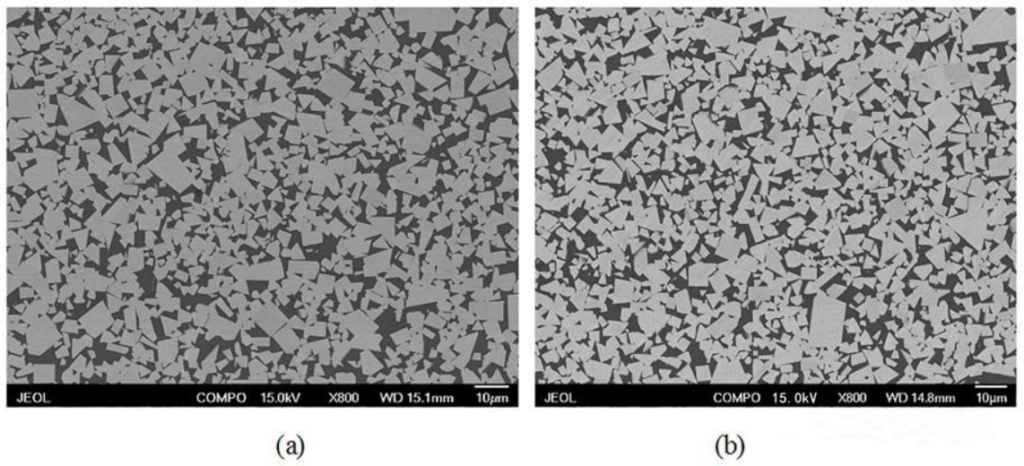
(b) YG20 極低溫処理後
極低溫処理前と比較して、極低溫処理後の YG20 の面心立方コバルト (fcc) は大幅に減少し、ε- Co (hcp) の明らかな増加も耐摩耗性と超硬合金の総合特性。
5.極低溫処理プロセスの限界
米國の工具?金型メーカーの実用化実績によると、処理後の超硬インサートの壽命は2~8倍に伸び、処理後の超硬伸線ダイスのドレッシングサイクルは數(shù)週間から延長されます。數(shù)ヶ月に。 1990年代に入ると、超硬合金の極低溫技術(shù)に関する國內(nèi)研究が行われ、一定の研究成果が得られました。
一般に、超硬合金の極低溫処理技術(shù)に関する研究は現(xiàn)在のところあまり発展しておらず、體系化されておらず、得られた結(jié)論も一貫性がなく、研究者によるさらなる詳細な調(diào)査が必要です。既存の研究データによると、極低溫処理は主に超硬合金の耐摩耗性と耐用年數(shù)を改善しますが、物理的特性には明らかな影響はありません。