Common Failure Phenomena of Tungsten Carburo Roll Rings
Sand Holes Inside the Roll Ring
The production process of tungsten carbide cemented carbide roll rings generally includes hot pressing, cold pressing, hot isostatic pressing, and cold isostatic pressing to achieve the densification of the internal structure of the roll ring and ensure its wear resistance and sufficient strength. However, due to various factors during the production process, sand holes similar to those produced by casting processes can occur within the roll ring’s structure, leading to failure in use. When slotting or grinding the roll rings, we often encounter this phenomenon. The sand holes vary in size; smaller ones can be eliminated by increasing the grinding amount during the roll ring processing, and their elimination does not affect the use of the carbide roll ring. Larger sand holes cannot be removed by general grinding and sometimes require abandoning a particular roll groove during processing. If the sand hole is located exactly in the middle of the roll ring’s width and is large, the roll ring can only be scrapped.
Cracks at the Bottom of the Roll Ring Groove
Under normal production, each rolling groove can guarantee a certain amount of rolling. However, some carbide roll rings wear too quickly during the rolling process and fail long before reaching the rated rolling amount. During inspections, it can be found that some roll rings have regular nail-like microcracks at the bottom of the rolling groove (see Figure 1); while others may have a craze pattern. These two types of cracks are dangerous for carbide roll rings. If the roll is not replaced in time, the cracks will expand, leading to the scrapping of the carbide roll ring.
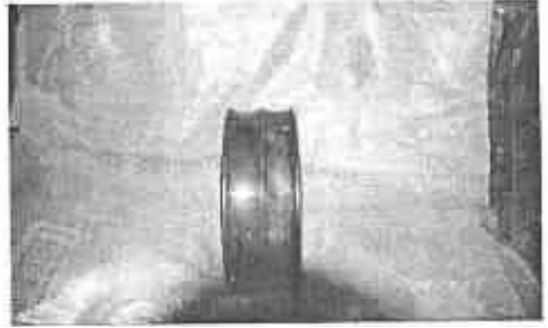
Roll Ring Bursting
During the production process, there are two phenomena of roll ring bursting: circumferential fracture and radial fracture. In circumferential fractures, cracks occur at the bottom of the roll ring’s axial hole grooves and spread in a ring shape along the rolling groove; in radial fractures, the roll ring cracks radiate radially. In production practice, circumferential fractures of roll rings are relatively rare, with most occurrences being radial fractures (see Figure 2).
Roll Ring Shattering
Shattering of roll rings is another major phenomenon of roll ring failure and is a more serious accident that occurs during the rolling process. The hazard of roll ring shattering is extremely high because during the rolling process, the rolling mill operates at high speed, and the explosive fragments of the roll ring can damage other roll rings, leading to the expansion of the accident. When a carbide roll ring shatters, fragments often strike and injure the carbide roll rings of adjacent frames, damaging the taper sleeve and aluminum cap.
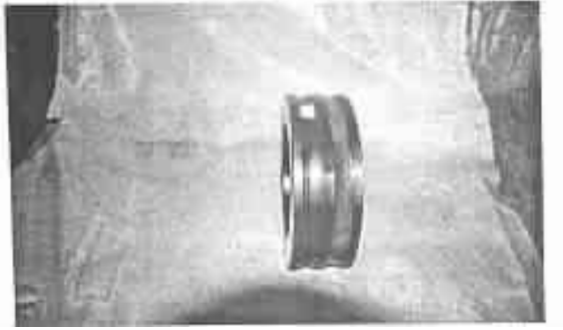
Analysis of Roll Ring Failure Causes
Cracking Due to Repeated Thermal Stress
During the rolling process, the hot rolled piece comes into contact with the surface of the rolling groove, causing the temperature of the roll surface to rise. This part of the metal will expand, while the metal temperature in the deeper layers of the roll rises less, resulting in compressive stress on the surface metal of the roll. Conversely, when the roll surface is quenched by cooling water, the surface metal contracts, while the deeper metal does not contract as much as the surface metal, creating tensile stress in the surface layer. This repeated alternation of thermal stress easily generates thermal fatigue cracks, causing the roll ring groove bottom to appear nail-like microcracks and crazing.
Optimizing Cooling Water Pressure
Insufficient cooling water pressure is also one of the causes of carbide roll ring fatigue cracks. To reduce the cracks caused by fatigue, it is necessary to use cooling water to carry away the heat obtained from the rolling piece, thereby reducing the temperature rise of the roll ring and the thermal expansion of the surface metal. When the rolling piece comes into contact with the roll ring surface, the surface metal of the carbide roll ring can reach 500~600°C. When cooling water is sprayed onto the hot roll ring surface, it forms a layer of steam film that covers the underlying roll surface, severely affecting the cooling effect. Studies have shown that when the pressure of the cooling water is less than 0.5MPa, it cannot break through the steam film, and even with sufficient water volume, the desired cooling effect cannot be achieved.
Maintaining Water Quality
Water quality can have a significant impact on the life of the finishing mill roll rings. Tungsten carbide roll rings have special requirements for the acidity of the water quality. Generally, acidic water quality can cause corrosion of the hard alloy rolls. When the pH value of the water is below 7, the cobalt alloy begins to corrode, exacerbating the propagation of thermal cracks and greatly reducing the life of the roll rings. Therefore, in addition to maintaining cleanliness, the acid-base balance of the water must also be maintained.
Quality, Operation, and Production Factors
The circumferential fracture of the roll ring is mainly caused by the propagation of fatigue cracks, while the reasons for the radial radiating fracture of the roll ring are more complex. Summarizing practical experience, the following are several causes of radial fracture of carbide roll rings:
Material Deviations and Sintering Process Defects
There are issues with the quality of the roll ring itself. The material formulas of roll rings produced by different manufacturers are distinct, resulting in different grades of roll rings. Even carbide roll rings of the same grade produced by the same manufacturer may have deviations in material proportions, leading to unstable quality of the roll rings. Another reason is that during the manufacturing process of the roll rings, improper control of the sintering process parameters can lead to defects in the quality of the carbide roll rings. We have experienced continuous radial fractures of roll rings provided by a domestic manufacturer, and the manufacturer admitted that there were issues with the sintering process after analyzing the causes of the accident together.
Overlooked Process Requirements and Excessive Pressure
Improper operation during roll mounting. There are clear process requirements for the mounting and dismounting of finishing mill roll rings, but in the production process, operators often overlook these requirements in order to work faster, resulting in insufficient cleaning of the roll rings and the taper sleeves. Moreover, operators may not control the pressure properly when using the roll mounting cart, and excessive pressure can easily cause roll ring fractures during the rolling process. Additionally, if the temperature of the roll box shaft head is not sufficient when the operator mounts the roll, it can also easily cause roll ring fractures during the rolling process.
Taper sleeve quality issues
Because the inner surface of the taper sleeve contacts the roll shaft of the roll box, and the outer surface contacts the inner surface of the roll ring, the process requires high precision in terms of concentricity and ovality. If the concentricity and ovality are out of tolerance, uneven contact between the taper sleeve and the roll ring can cause local stress during production, leading to carbide roll ring fractures.
Steel stacking
It is inevitable that steel stacking accidents occur during production. If such an accident occurs in the finishing mill, it can cause significant damage and harm to the roll rings, as the rolling pieces are rolled at high speed with temperatures above 1000°C. When steel stacks, the metal accumulates around the roll ring groove, and due to high temperatures, the metal adheres to the roll ring surface, forming a “turtle shell” phenomenon. At this point, the local heating of the roll ring generates thermal stress, easily forming thermal fatigue cracks, which can lead to fracture failure when the roll ring continues to be used.
Conclusión
The reasons for roll ring shattering are also multifaceted. Generally, it is an expansion of the roll ring fracture accident, as the roll ring fractures while the mill is still operating at high speed, and the tremendous centrifugal force causes the fractured roll ring to break apart. Another reason is the impact of the rolling piece on the roll ring